Prototype Tool Manufacturing
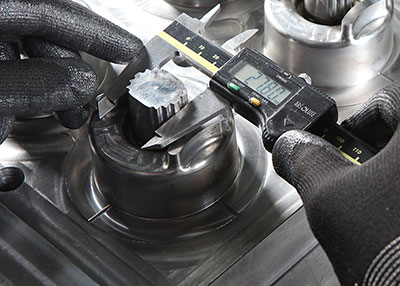
The elastomer technology in the field of NVH has basically three categories of molding: Compression, Transfer and Injection. The most appropriate mold design is made considering the conditions such as the product's geometry, chemicals inside of the rubber and the production technology.
Shrinkage value is very important in volume molding technology. Mold design needs to be made considering the finished part and expected mechanical properties. The part that comes out from the mold cavities and creates internal stresses when the surface temperature is left to cool down. Mold design needs to be made considering the finished part and expected mechanical properties.
We are not only manufacturing vulcanization tooling; in addition, plastic, aluminum injection, metal forming, and assembly toolings are designed and manufactured.
Each study and experiences in process noted as lessons learned and is standardized by adding to the Tooling Development Instruction.
Serial Tool Manufacturing
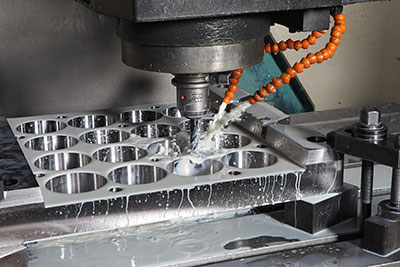
Mold design is at least as important as product design. One of the issues to be considered when designing molds is the correct formation of the flow path of the rubber, where rubber flows in ~150°C mold plate.
The number of cavities of serial tooling depends on the number of annual production, part size, press pressure. Especially when the number of cavity is increased, it is important to distribute the pressure to be applied to the mold and to flow the rubber regularly on the runner. This requires a very good gating and runner analysis. Parameters such as runner, injection holes, tool materials, the surface roughness are the parameters to be analyzed separately, which are huge effects on finished product.
Designing the flow of the rubber in the mold and preventing turbulence during the flow results in serious consequences on the finished product.
Keeping the rubber in the mold and preventing the rubber to escaping from the runner has a huge effect to keep pressure under control and avoid waste of rubber.
Considering different materials such as steel, aluminum and plastic, the hardness value of each material is different. Therefore, the form and depth of sinking are determined according to the material. Otherwise, it is necessary to make extra effort for cleaning the product from the mold.