Test Capabilities
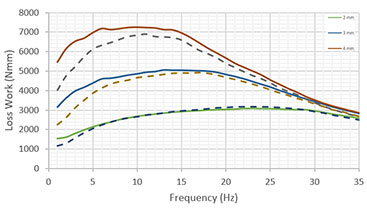
In development phase, it is important to consider not only the product but also the components it interacts with. Knowledge and competencies in this field have huge effects on development. With the benchmarking analysis, the current situation of the product and state of Technologies are determined and they are taken as an input for specification. Thus, all boundary conditions are simulated, which the part may exposed.
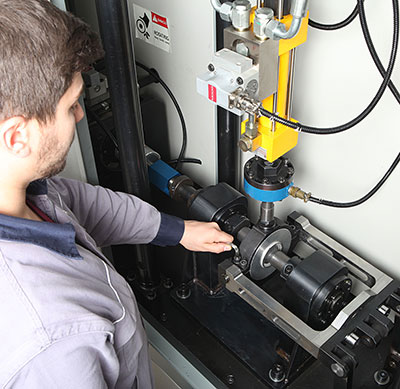
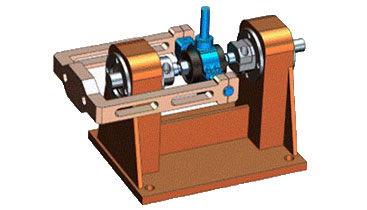
Test specification is usually created according to the static conditions for conventional bushings. However, in anti vibration elements such as hydro-bushing and engine mount; dynamic values are very critical like dynamic stiffness, damping, loss angle etc. Durability performance is key value for any kind of NVH problem.
Prototyping
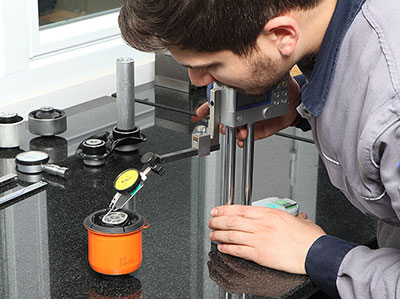
Elastomers have viscoelastic structure, which has non-linear characterization. For this reason it is not so easy to make material modelling on FE studies. Therefore it is important to verify every FE analysis results with a prototype to make a correlation between virtual and real values.
Prototype mold production is done in a very short time in our prototype workshop. The prototype part is the first step in mass production and gives information about the accuracy of the design.
In addition to dimensional controls, physical tests are performed on the produced prototype parts and the results are examined. Especially, we can check durability performance of parts, which is very serious criterion of NVH problems.
YAMAS has two laboratories as quality and R&D and one section for chemicals analysis. We perform push in, bonding, stiffness characterization tests for mass production approval, which are carried out in these laboratories. In the development phase, all dynamic values in the frequency band are tested and 100% durability test is performed for each project. All test fixtures are designed and manufactured at tool shop, which are used for characterization test.
On the other hand, all test results are used for rubber formula optimization. TGA and DSC tests are also performed for formula details as reverse engineering method.
We are working with technical university for FTIR analysis to determine the chemical components of hydroil for hyrobushings.